How Expert Packaging Maker Repair Solutions Reduce Downtime and Increase Performance
Specialist product packaging equipment repair work services are important in reducing downtime and boosting productivity via specialized diagnostics and prompt interventions. The ramifications of such services expand past immediate repairs-- unloading the wider influence on functional efficiency exposes essential insights into long-lasting productivity approaches - packaging machine repair service.
Relevance of Timely Repair Works
Prompt repairs of product packaging equipments are important for keeping functional effectiveness in any type of manufacturing atmosphere. When equipment malfunctions or breaks down, it can bring about substantial disturbances in manufacturing lines, leading to increased downtime and shed profits. The longer a packaging device continues to be out of commission, the better the effect on general performance, potentially triggering hold-ups in meeting orders and diminishing customer contentment.
Along with the immediate financial implications, delayed repair services can result in a lot more extensive damage to the equipment. Components that are not resolved quickly can deteriorate additionally, calling for even more expensive fixings or full replacements, which might have been avoided via prompt intervention. Additionally, regular maintenance and prompt repair work can boost the life-span of product packaging equipments, making sure that they run at optimal efficiency levels.
Spending in specialist product packaging equipment repair solutions is essential for minimizing these risks. A proactive strategy to fixings not just preserves production routines yet additionally fosters a society of reliability within the company. By focusing on timely repair services, services can maintain their affordable edge, maximize source allowance, and ultimately boost their profits with improved functional efficiency.
Competence in Diagnostics

Reliable diagnostics not only help with speedy recognition of problems but likewise improve the general dependability of product packaging procedures. By carrying out thorough examinations, professionals can assess the health and wellness of important components, guaranteeing that even minor irregularities are dealt with promptly. This focus to information lessens the danger of unexpected malfunctions, which can bring about pricey downtime.
In addition, expert diagnostics supply important insights into operational fads, allowing companies to make educated decisions pertaining to equipment upgrades or adjustments. By leveraging these understandings, firms can enhance their packaging procedures, leading to enhanced effectiveness and productivity. Inevitably, buying analysis experience is necessary for organizations looking for to keep smooth procedures and support high criteria of high quality in their packaging procedures.
Preventive Upkeep Benefits
Preventative maintenance matches professional diagnostics by proactively attending to possible concerns before they manifest into major issues. By carrying out a structured precautionary upkeep program, firms can substantially reduce the threat of unexpected device failings, therefore decreasing pricey downtime. Normal inspections, cleansing, and components substitute help guarantee that packaging machinery operates at ideal performance.
Among the key benefits of precautionary maintenance is its ability to expand the life expectancy of devices. By on a regular basis preserving equipment, services can stay clear of the compounding effects of wear and tear that frequently bring about significant repairs or replacements. packaging machine repair service. This not just saves funding however also boosts the overall dependability of manufacturing processes
In addition, precautionary upkeep adds to boosted security problems within the work environment. By recognizing and correcting prospective dangers prior to they escalate, organizations develop a much safer environment for their employees. This positive technique not only secures employees however likewise fosters a society of obligation and caution.
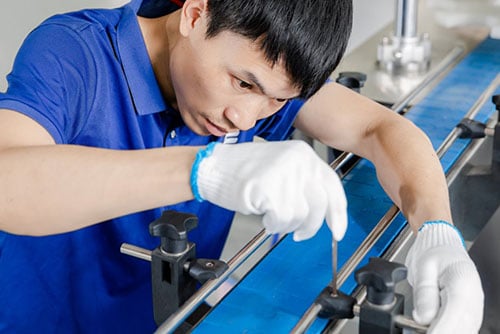
Customized Service Solutions
Acknowledging the unique demands of each company, tailored service solutions for packaging equipment fixing offer customized approaches that improve operational performance. These remedies are developed to address certain challenges encountered their website by various markets, ensuring that maker downtime is lessened and productivity is taken full advantage of.
Professional repair service solutions start with a detailed evaluation of a business's packaging procedures. By comprehending the details machinery included and the needs of the production environment, professionals can develop a customized repair and maintenance plan. This may consist of specialized training for internal staff, the implementation of anticipating maintenance modern technologies, or the stipulation of dedicated assistance during height manufacturing times.
Additionally, personalized options can include adaptable service arrangements that line up with a business's functional schedule, enabling repair work to be done throughout off-peak hours. By prioritizing the one-of-a-kind requirements of each organization, these bespoke services make certain that repair services are not just reliable yet likewise perfectly integrate right into existing operations.
Eventually, the concentrate on customization allows firms to enhance their packaging processes, leading to boosted integrity and efficiency of equipment, which is important for keeping competitive benefit in today's fast-paced market.

Effect on Overall Performance
Personalized solution options not just address certain fixing requirements yet likewise play a considerable function in enhancing general operational efficiency. By giving targeted interventions, specialist packaging machine repair service services directly reduce the frequency and period of tools failings. This proactive method makes certain that manufacturing lines continue to be operational, decreasing interruptions that can result in pricey downtime.
Additionally, efficient fixing pop over to these guys services add to smoother process, as well-kept machinery operates at ideal efficiency degrees. When machines work correctly, the quality of packaged items enhances, leading to fewer problems and much less rework. This improvement not only increases productivity yet also enhances client fulfillment.
In addition, normal maintenance and fast response times from fixing specialists cultivate a culture of reliability within the organization. Employees can focus on their main jobs instead than stressing over potential devices breakdowns. The general throughput of the production process increases, allowing firms to meet demand a lot more effectively.
Ultimately, the calculated investment in expert repair solutions converts to improved effectiveness across all operational facets, making certain that organizations can adapt and thrive in an open market. This harmony in between maintenance and productivity is vital for long-lasting success.
Conclusion
In final thought, specialist product packaging machine fixing services play an important function in reducing downtime and improving performance within making environments. Timely repair work, specialist diagnostics, and preventive maintenance add to the dependability of equipment, while customized solution options address details operational requirements - packaging machine repair service.
Comments on “Packaging machine repair service for emergency and immediate repairs.”